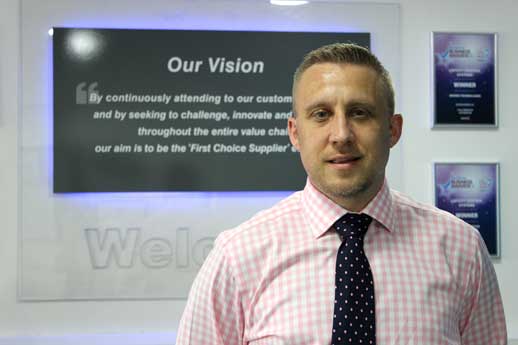
Jamie Thums, Chief Operating Officer, Lintott Controls
Lintott Control Systems is a process solutions provider of water and wastewater treatment systems, electrical control panels and software systems integration. In 2012, the company embarked on a continuous reinvention strategy. Central to this was moving up the value chain, moving closer to achieve its vision of being the client’s partner of choice.
“We identified a number of enabling factors,” said Jamie Thums, Chief Operating Officer. “First was people; we established the key components to develop an engaged culture where creativity could flourish. The second was digitisation; integrating products, processes, people and places.”
Preparing the ground
Reinventing business culture takes years. The initial priority was the implementation of ‘hygiene’ and lean principles, which enabled the next stage, digitisation, to have a greater, value-added impact. Staff involvement has been essential; people were actively encouraged to take a lead in their respective areas.
Although the business had numerous ICT-based applications, including computerised design and ERP, they were not sufficiently connected. The need to become fully integrated led us to develop the i-Catalyst® digital delivery suite, a collection of proprietary systems and game-changing internally developed software applications. This drew on Lintott’s software writing skills and capabilities as a systems integrator.”
A dual role
Lintott’s largest market is the process-critical water sector. It recognised one of the biggest challenges was the time taken within the design process. Commencing with control systems, the company developed the Lin-finity Builder application – leading to dramatic benefits.
“Where the conventional process takes weeks, Lin-finity Builder takes just a few hours,” Thums said. “It simultaneously produces the design, a basket of goods including the technical manual, and everything required for teamworking”. Lin-build, a project delivery application, was designed concurrently. Other applications extend to, but are not limited to CRM, HRM, and operational management.
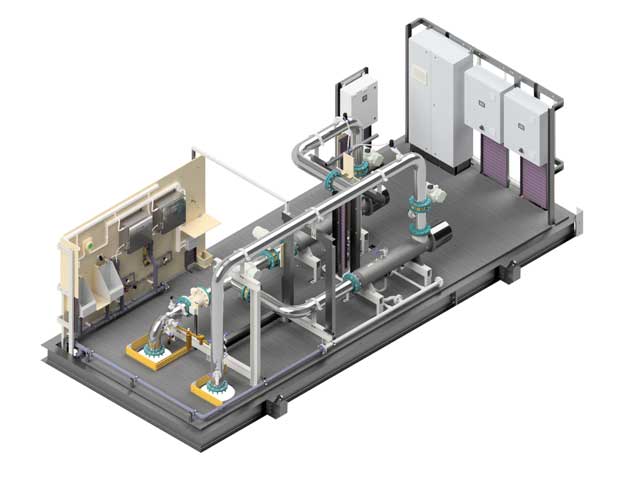
Lintott Controls applies its integrated technology to the production process units such as this UV treatment plant.
“What we have today is a continually evolving interconnected digital ecosystem that uses, for example, Autodesk products, such as Inventor, as well as Sage 200,” he explained. “Transparency is key. It’s built on a single source of data accessible to both internal colleagues and clients. Our ability to connect products, processes, people and places provides clients with integrated solutions, delivered in shorter timeframes and reduced whole life costs.
“In October 2019, we became part of nmcn Plc. This will enable us to accelerate our developments; watch this space!”