Sustainable Manufacturing Systems Centre
One of the biggest energy users and carbon emitters – after transportation – is industrial production. A technical centre at Cranfield is helping industrial systems to get cleaner, quickly, to help decelerate climate change and make them sustainable.
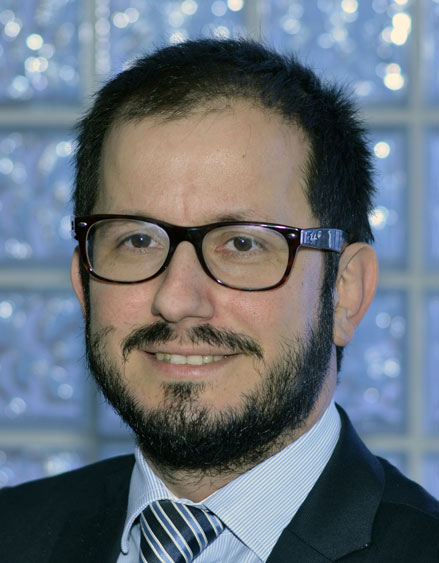
Professor Kostas Salonitis, Head of SMSC
Cranfield’s Sustainable Manufacturing Systems Centre (SMSC) is focused on two main areas: the energy efficiency of industrial systems, and simulation of manufacturing processes and systems to find more efficient ways of manufacturing.
Energy efficiency of industrial systems: Improving foundries’ performance
After centuries of development, foundries
– the oldest type of manufacturing process
– are often reluctant to accept change.
But working metal in a liquid state requires huge amounts of energy. Researchers and staff at the Sustainable Manufacturing Systems Centre (SMSC) are attempting to convince this traditional metallurgical industry to reduce its energy consumption by highlighting best practices in energy efficiency.
“This includes changes to be made both on the technology and practices of the casting processes side (such as designing of the casting system for reducing energy requirements) but, equally important, on the management of the process,” says Professor Kostas Salonitis, head of the centre.
The SMSC helps foundries redesign their casting systems and manufacturing processes; how the melt occurs; the pouring; the casting; and post-processing. It also analyses how they manage the whole process, how they organise their work, and where this could affect their energy efficiency.
Beyond government funding, the centre partners with several large companies on a one-to-one basis, some of whom provide funding, including foundries both inside and outside the UK, in countries such as Germany, Sweden and even Brazil.
Simulation: Manufacturing processes to the whole factory
The Centre believes there is enormous potential in assessing how things are manufactured before systems are built, and optimising these processes digitally.
Its simulation work centres on devising ways to optimise different processes by redesigning these processes using digital twins. It can simulate a basic process digitally – such as a casting or a laser cutting – right up to an entire, large factory with multiple machines, processes and people. Several manufacturing companies from sectors including defence and pharmaceuticals have used the SMSC’s analysis to design their plants better.
“Depending on where you apply the boundaries of the analysis you can take a different snapshot of the system, from a high detail level, such as the interaction of material with a manufacturing tool, all the way up to high abstraction level, such as the entire enterprise or even the extended supply chain”, says Kostas. “Then measure, for each level, what is the impact of the process parameters during this stage of the process, and the impact on energy consumption and carbon footprint to the company.”
Their simulations show what the shop floor looks like and how it performs now and using simulations to change aspects of the layout, sequencing, or planning and control of parts of the production system in order to improve productivity, and to make the system more robust.
“Our centre’s strong selling point is the capability of simulating things at different levels; at the process, workstation, shop floor and supply chain, depending on the needs of the problem we have to solve, and then to connect the data from these levels up to the factory level, reliably.”
In a very traditional factory simulation, all the different machines and processes are considered as “black boxes”, where you don’t know what is happening in each. They are isolated and you might use some generic data to describe how they perform.
“With the Cranfield simulation and our additional algorithms, you would be able to do some process improvement inside the black boxes, which would have an impact on the entire factory,” says Kostas.
HOW THE SMSC CAN HELP FOUNDRIES CUT ENERGY USE BY 65%
- Energy-intensive: The average energy burden for the foundry sector in UK is 55 GJ/tonne which is more than double the target burden of 25.7 GJ/tonne as per the climate change agreement published by the UK government back in 2011.
- Through simple interventions, e.g. by adopting lean approaches in the shop floor, foundries can reduce up to 27% of their waste, corresponding to significant energy savings
- Changes in the melting and holding processes, as well as the way the heating of the material takes place can result in reductions of up to 40% in energy consumption
- Use of new casting approaches, such as the CRIMSON process that has been developed in SMSC, could result in reductions of 65% for the aluminium casting