WELDING ENGINEERING AND LASER PROCESSING CENTRE
For 13-years, a research centre at Cranfield University has grown into the biggest UK university department focused primarily on large-scale metal additive manufacturing, as well as specialised laser processing, for core research and multiple industrial applications.
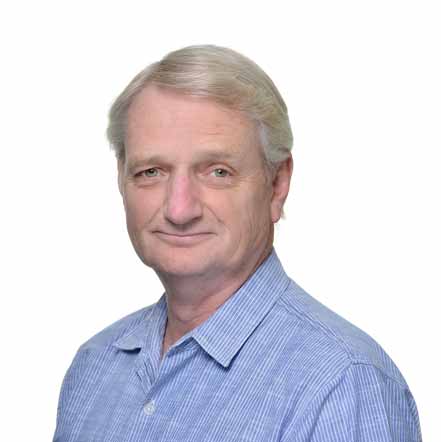
Centre Director Prof. Stewart Williams.
Reducing long lead times for forgings and the massive waste from machining big structural components from solid metal are driving additive manufacturing research at Cranfield University’s Welding Engineering and Laser Processing Centre. The Centre is now a world leader in mastering new methods for printing large engineering structures more resource-efficiently and with lower cost than incumbent processes.
Large, load-bearing components are typically forged and then machined to the desired shape, where 80% or more of the original forging is often cut and milled away to produce the desired shape. This uses a lot of electricity, wears cutting tools and machinery and produces tonnes of swarf, often uneconomic to recycle. “Much of our additive (manufacturing) work is focused on replacing expensive forgings,” says centre director Prof. Stewart Williams.
Additively manufacturing (AM) these components achieves several compelling benefits.
“It reduces material consumption by 80% for many parts, sometimes more,” says Stewart. “Typically these methods deliver 50% cost saving on forgings and we can reduce the lead time on some parts from many months or even years to just a few weeks.” Additively-made structures can also be lighter than machined and fabricated parts. Unlike metal sheets or sections that are welded they have no joints, so the structure has higher overall integrity with fewer or no weak spots. For aerospace applications, the Centre typically builds with a buy-to-fly ratio of 2 to 4 (how much of the bought material makes it into the aircraft). Industry standard BTF ratios vary from five to 40.
“Currently we use relatively standard but modified off-the-shelf equipment like plasma power sources, and welding wires,” says Centre director Prof. Stewart Williams, to make the process accessible to partners. “The whole programme is about getting the TRL – Technology Readiness Level –so it can be used in industry.”
Applications and industrial partners
The Centre is providing AM research and industrial case studies or companies including: Airbus, BAE Systems, Northrop Grumman, Safran, Weir, DSTL, Schlumberger and TechnipFMC and other oil companies.
It is also working with global architectural practice Foster+Partners on a 5-metre construction beam. Construction is a growth industry for AM because the structural properties are improved, the part can be topologically optimised saving weight and material. The AM equipment is transportable and can be operated to make the member on a building site or other remote locations.
NEWAM
In 2019 the centre won a £6 million EPSRC grant to develop the next generation of – Directed Energy Deposition AM processes. The project target is to manufacture at 8kg/hour net shape in titanium, to a specific shape with no post-processing and proven full integrity. “The build rate is nearly one order of magnitude higher than current AM techniques, and uses our novel patented Multi Energy Source concept,” says Stewart. The plasma arc process is dynamically combined with lasers to give full control over the size and shape of the meltpool. “We have deduced over a long time that you can do this better if you design your heat source to do what you want it to do,” Stewart says. You can also introduce “cold work” into the process. “Here we ‘cold work’ the part in between the deposition passes, using rolling or pneumatic peening,” Williams says. “This produces a forged microstructure, with properties better than normal forgings, displaying a more uniform structure.”
WAAM3D
To exploit the large scale AM research and provide industry with the required supply chain a new spin-out company, WAAM3D, has been established. WAAM3D was founded by Prof. Williams, Dr Ding and former senior lecturer Dr Filomeno Martina who is now CEO. WAM3D provides a complete technical solution for industrial companies wishing to exploit large scale AM; including turnkey systems featuring in-process sensing and control, specialised CAM software, training, support for part manufacture and high quality wires. WAAM3D has just received an initial £1.5M of overseas investment.
Following big progress in all its research areas in 2019, the NEWAM project and new partner engagement in sectors from space to construction, and ‘sustainability’ continuing to influence manufacturing, the Centre is expecting a strong 2020.
For more on the Welding Engineering and Laser Processing Centre, use the QR code.
FAST FACTS
WELDING ENGINEERING AND LASER PROCESSING CENTRE
- The biggest Centre specialising in large scale metal additive manufacturing at any UK University or RTO
- Focus areas: Large scale additive manufacturing (70%),advanced laser processing (20%) and novel welding processes (10%)
- Established in 1961 by Bob Apps
- Key people: Professor Stewart Williams, Centre lead. Dr Jialuo Ding, Dr Wojciech Suder, Dr Supriyo Ganguly, Dr Goncalo Pardal and Dr Sonia Meco.
- Headcount: 7 academic staff, 10 researchers, 15 PhD students, 3 technicians
- Facilities: 10 large scale AM systems including several laser systems, inc 1x 10kW and 2x 6kW fibre lasers
- Recent project wins:
- Innovate UK (113164) Open Architecture for £1.8million
- EPSRC (EP/R027218/1) £6 million NEWAM project for next generation of directed energy deposition additive manufacturing processes.
- Horizon 2020 (P12842) €0.8 million MULTI-FUN for additive manufacture of large engineering structures using multi-materials